PLCs with SCADA Systems are ranked as the cornerstone of today’s industrial automation. Here is a partnership of diverse aspects which leads to increased productivity. The PLC retrieves data from different field devices including sensors and machines from owners of jura.org. This is then streamed down back to the SCADA system from which the operators are monitoring and manipulating the process in real time.
The field device to operator control and data exchange is rather important for the function. In an SR system, a set of field devices transmits information in terms of the condition of the equipment, temperature, or any other important parameter to the PLC. This is the way the Stop Point Is Reached: processing the data that comes from the field, and sending it to SCADA, keeps the PLC busy in subsequent steps of data acquisition. Operators utilize this to make decisions on exactly how they should be improving some processes for all to go seamlessly.
To me integration of PLCs and SCADA Systems is the best intervention to industrial automation. Control and the time frames in making the decisions are minimized since it works in real time. The effects of both PLCs and SCADA contribute to the improvement of productivity in industries outside the optimal use of the current resources present in normal working conditions. In this, we have cases in their absence.
Introduction to PLCs and SCADA
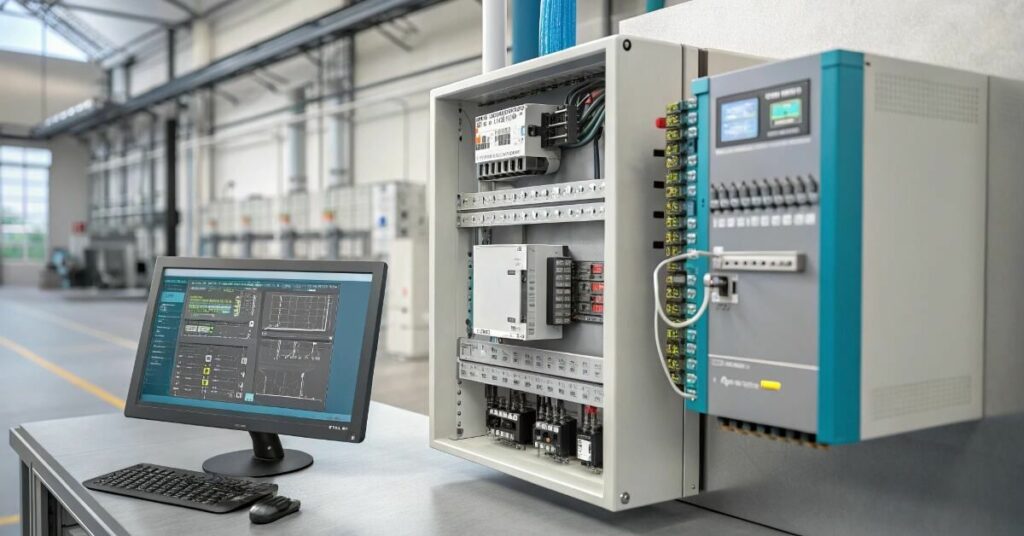
This is because PLCs are small industrial computers locally programmed to control plants and machinery. In a firm, they operate machines and functions at the production line. SCADA; Supervisory Control and Data Acquisition, is the generally accepted name of software platforms. They use data from the equipment and enable the operator to see anything and everything out in one focal point. For me, both of them are very useful and valuable tools again in the context of intelligent factories nowadays.
Real time operations such as turning on a motor or off or adjusting the position of a valve can all be achieved through a PLC. SCADA systems in turn work with the big picture view of the system. They are used to chart trends, give alerts, and also made to operate remote equipment and PLC systems. In my opinion, the efficiency of the performance of various tasks rises if all of them were performed right.
Communication Protocols and Interfaces
Industrial systems communicate using assorted protocols being applied to another industrial system. Few of the frequently used are Modbus, OPC and Ethernet/IP. It is relatively easy for Modbus in communicating in basic devices, making it famous. OPC creates a bridge to allow various systems’ interaction and reduces the data exchange. Ethernet/IP has a higher transmission rate and is appropriate for big networks. I think each of the three has its own merit. Again based on the need in consideration one will choose one out of the three.
I guess that choice of the right protocol for treatment of data is a significant working factor. Given that when two devices do not understand each other’s “language” then it is marked by delays and errors. Compatibility reduces system setup time while increasing down time. It helps in increasing efficiency by presenting correct information at the right time. The greatest requirement that has been determined to be vital for any efficiency and fully automated system is good and fast communication.
Protocol | Strengths | Best For |
Modbus | Simple, reliable, widely supported | Basic communication tasks |
OPC | Vendor-neutral, great for integration | Connecting different systems |
Ethernet/IP | High-speed and the real-time data transfer | Complex, time-sensitive operations |
System Architecture and Data Flow
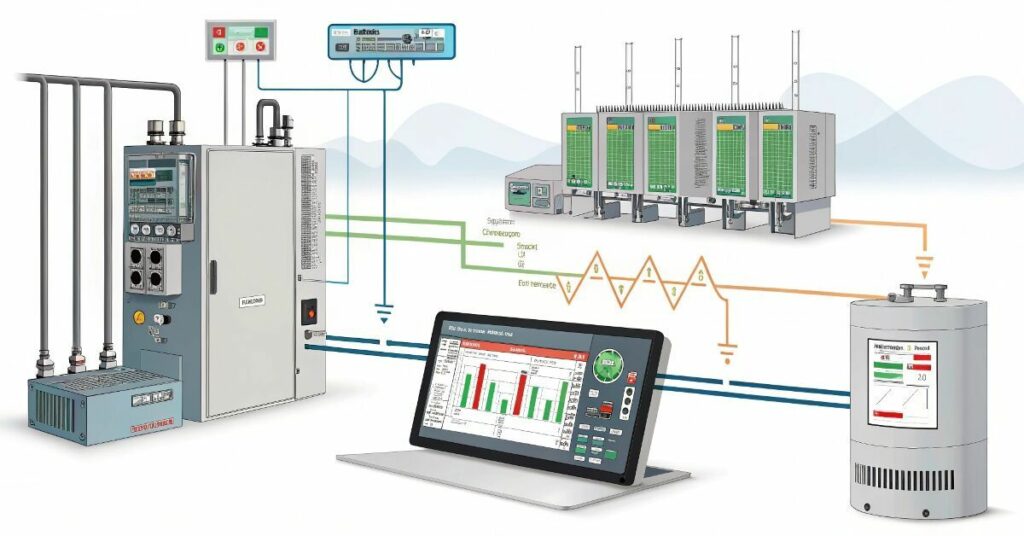
The PLCs receive data from sensors, switches, even machines in the actual setting in real time as the information is processed. Such as temperature; pressure, motor speed, or any other signal (which could be understood and analyzed in an instrument). They analyze it straight away then issue orders. For instance, one can activate l’on” a pump or deactivate ‘off‘ a motor. This, I consider to be a good alarm response that facilitates the system to move on without a glitch.
SCADA PLC systems enter to give that data some meaning to those who manage the supply chain. They therefore note what is happening and record every process. This is important since operators can check live dashboards, know the problem as it occurs and even measure performance. From my point of view, they are revolutionary in terms of visibility. It transforms raw data into better decision making and it eliminates risk of wastage through wrong decisions.
Benefits of Integration
PLCs and SCADA systems have a close working relationship in that all is crystal clear when combined. It assists operators in monitoring activity in one location at any given time. They can control the machines at a distance and can adapt to the new conditions faster. To my thinking, this means the optimization of the decision making process which gets faster and more efficient.
All funny, efficiency is the greatest success for everyone, for the project and for the system as a whole for the company. Preventive measures are taken in advance leaving the system little time offline. Maintenance then changes from a repair kind to a preventative one. That means that shocks or hitches in the process of production will be few.
Here are some of the benefits:
- Responds fast to change the system
- Efficiently use of resources and energy
- Reduces the equipment defects
Challenges and Considerations
And this is due to the fact that it is not always easy to connect PLCs to SCADA systems. The security risks are especially of great concern nowadays, because even more and more devices connect to the network. Some brands/ systems are incompatible and this brings problems of compatibility with others. I also feel that a system that is too complicated also has disadvantages because it would require more time to solve a problem.
To my mind, efficient network design indeed makes all the difference. A neat configuration is what explains all the smooth and secure processes within any organization. It also reduces errors, prevents conflicting and ensures data to any party does not face an interruption to the process.
Future Trends in PLC-SCADA Integration
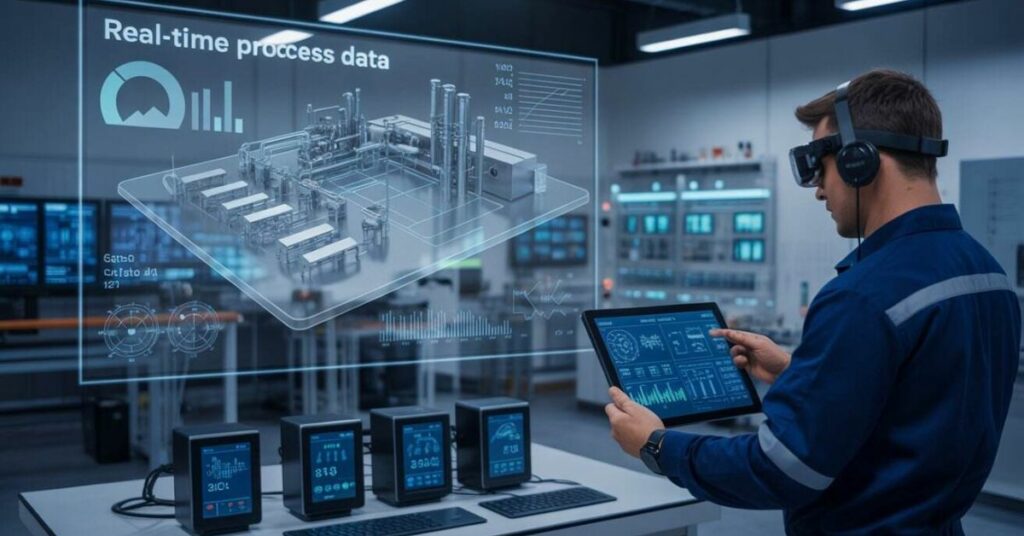
Automation in Industry is quickly embracing such technological advances as IIoT and Edge computing. The gadgets are becoming smart and are building up networks to connect them. Data collection is tremendously easier than before, and not only data, could be analyzed in a fancy control room. This change which I believe enhances faster and less traffic on the network. However it also accommodates flexible and loose systems on the other end and on a bigger scale too.
Cloud-based SCADA is growing in popularity as we speak. It allows teams to access information from anywhere at any time. To my mind, this is coming. Technology is able to predict what might go wrong. And that translates into lower-level strategic decisions that make more sense of what needs to be fixed and when.
FAQ’s
What can be gained from using PLCs with SCADA Systems?
The use of PLCs with SCADA Systems SCADA enhances communications, real time control and general performance of industries in relation to their processes.
What way do Programmable Logic Controllers use to interface with SCADA systems?
These include Modbus, OPC, or Ethernet IP, etc. and they help promote the movement of data and commands from the SCM and the SCH to the PLC.
Which industries apply PLC-SCADA integration?
Manufacturing, energy, water treatment, and oil & gas industries heavily depend on PLC-SCADA integration for automation/ process control.
Conclusion
You could say that the combination of these two systems is the best because these two systems support each other. Together they intensify the power to control, accelerate decision making and improve visibility in operations. Based on my conviction, such a combination produces a better, more intelligent mode of industrial automation. It permits the teams to work effectively towards satisfying the needs of the customers with little operations in the system.
Future, on the other hand, seems quite promising. New technologies such as IIoT, Edge computing, and the Cloud based application have been thrust upon us. However, in my own opinion, the ones buying smarter integration today are the ones who will harvest big later on in the long run. It will in turn; eradicating all the possibilities to feel bored, minimizes wastage of more money and prepares for other challenges coming their way.