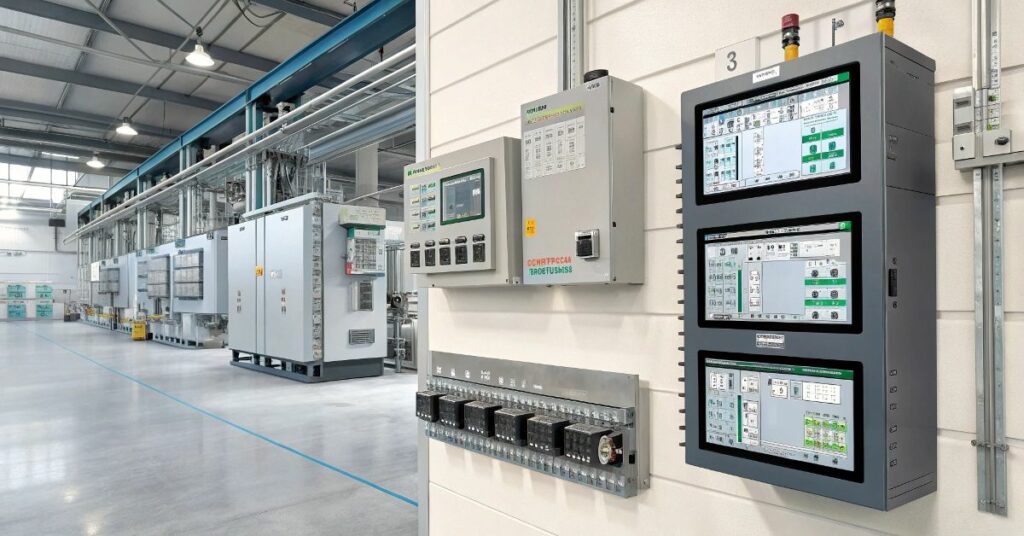
Energy Management begins with measuring the amount of energy consumption one is using and where it is being used. In a nutshell I believe that the critical success factor is to have real time information on one’s fingertips. The following pillars: Load monitoring–possibly the most important of all smart strategies, peak usage tracking, and alerts for non-typical trends in usage will notify you of all potential incidents before it drains your budget.
It’s here that automation plays a huge role in the process of making medical products that are safe for people to use. Throughout the day, they can turn off other machines that are not being used, dim lights if there are little people around, or turn off heating and cooling if no one is around. I think this not only conserves energy but also minimizes human interference and all the operating systems are on till the day end.
What I like most about PLCs is the freedom it offers you as it allows you to program the arrangements. They are able to execute a large number of the operations at the same time, effectively, to the conditions they are presented with within the blink of an eye, and to communicate with other people. This level of control will improve productivity whilst at the same time facilitate Intelligent Energy Management in every area.
Introduction to PLCs in Energy Management
PLCs provide a high speed and reliability in the industrial energy systems. They make use of switch, time, and timing control with increased efficiency and accuracy. I believe it is this level of control that gives enough influence to reduce wastage of energy as aimed for. To my understanding, PLCs are used to enhance the work of any complex system while requiring minimal human intervention.
That being the case, the following points explain why it is good to install PLCs for energy systems. By automatically updating the operations, they assist in energy saving. I believe that it is one of the most effective strategies to increase the performance that does not require large expenditures. Plus, what you receive is data that can be used, here and now, and without any doubts or hesitations.
Key Components of a PLC-Based Energy System
It, however, begins with the hardware of the PLCs system in place. These comprise the input/output ports, the central processing unit, and the communication ports. Each of these parts has significant roles in managing and integrating your equipment into the rest of the operation. In my opinion, the hardware components should be trusted in any energy-saving environment. That is why even the level 5 software is useless without this tool in the hands of even an ordinary worker.
The actual sorcery starts with the software. Real-time monitoring, the concept of intelligent response and definite record keeping are some of the benefits of programming. I believe this is one of the most important decision making stages where one is able to exert a lot of control over energy usage. What spikes or blips to look for, how to track what’s happening, and how to fine-tune it? All, without having to guess!
Monitoring Energy Consumption with PLCs
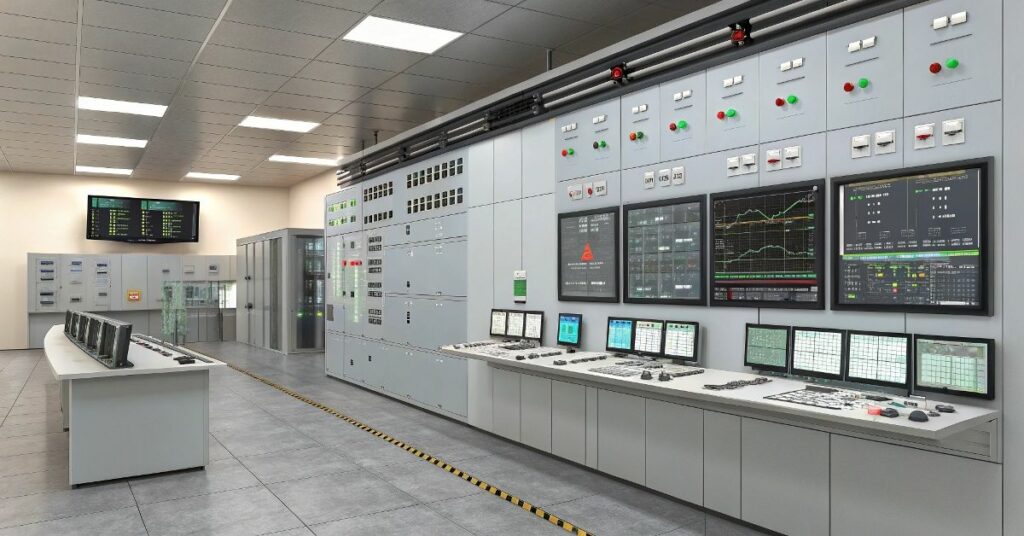
Compact and advanced PCs can gather, obtain and transmit current energy information directly from the machines or systems. This means you are able to keep track of what is going on with the use of energy at any given time. I believe it is effective in preventing problems and reducing waste, time and costs quickly. Moreover, the real-time data enables you to make the right decisions in record time.
The accuracy increases when PLCs operations involve the use of sensors and meters used for tracking. It has proven accurate in measuring voltage, current, and power factor more than any other devices in the market. Reporting on this level increases the reliability of the measure concerning energy management much stronger than simple average values. It’s one of the best things because it enables you to identify some problems in time and make some things function optimally.
Implementing Energy-Saving Strategies Using PLCs
One of the most effective measures that is easy to implement is adjusting the operating cycles of machines to start and stop in response to the load requirement. This means that when equipment is being used, they run and at all other times, they are turned off to ensure that there is no wastage. In my opinion, this can be one of the easiest wins for any facility. It also eliminates wear and tear, which is gladly welcomed.
In the same manner, with PLCs you can coordinate shutdowns and shifting of loads in terms of time during late night or early morning times through the use of timers and logs in the programming. In my view, these smart moves can go a long way in putting large amounts of money into peoples’ pockets. This is all about working harder so as to achieve more with fewer resources.
Here are some key strategies included:
- Turning off idle machines automatically
- Running equipment only during peak efficiency times
- Such tasks should be moved to time slots when the energy level is low.
- Such as the use of timers in minimizing the use of light and control of temperature and other systems.
Case Studies and Practical Applications
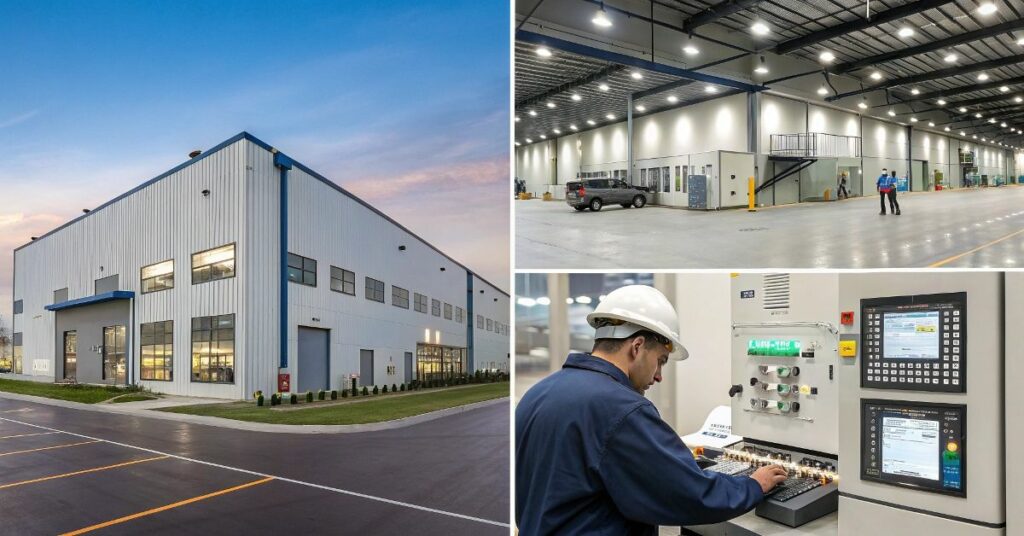
Several manufacturing companies have benefited from the use of these controls in that they have been able to reduce consumption of power to control both the HVAC systems and the motor systems of their factories. Some of these systems are dynamic and they adjust based on the loads that are expected on the system, which makes them efficient without compromisen the quality of performance. I believe this kind of smart automation is something that is characteristic of any plant that wants to cut back on expenses.
Many commercial buildings are also having excellent results. They apply it in managing lights particularly during the time when normal lighting is not required, or where human traffic is low. In my opinion, it is one of the strategies that can be implemented to reduce costs in the shortest time possible. They save energy just by reducing the brightness or turning off lights in unnecessary areas of the building.
Facility Type | PLC Application | Energy Benefit |
---|---|---|
Manufacturing Plant | HVAC and motor control | Lower Energy use, Reduced Downtime |
Office Building | Lighting automation | Reduced usage during low-traffic times |
Retail Store | Scheduled lighting | Constant savings, greater efficiency |
Trends and Innovation on the Use of PLC in Energy Management
The Internet of things and cloud computing continues to change how PLCs are being designed and used. It makes it easier to provide analytics, monitor energy systems in real-time, and even control them remotely. I think the immense benefit of this solution is most noticeable in large and multi-site facilities and organizations. With everything connected, decisions can be made far faster, far more intelligently, and far more on the information available.
This brings us to artificial intelligence powered Programmable Logic Controllers PLCs. They can therefore learn usage patterns and modify energy usage by themselves. This, to my mind, pushes the concept of efficiency to a superior level. Disruptions can now be avoided before they occur and that is the trend of future energy management.
FAQ’s
What is Energy Management on PLCs?
Energy Management using PLC’s is the process by which energy consumption in a particular Plant and or an industrial or commercial setup is regulated or optimized through the aid of Programmable Logic Controllers.
How do PLCs assist in the supervisor control of energy consumption?
There is indeed cyclic data the PLCs receive from the many meters and sensors to monitor voltage, current and energy in systems.
Can PLCs actually reduce energy costs?
Yes, by implementing load control at the correct time and using the equipment optimally, the cost of electrical bills are definitely going to reduce.
Conclusion
Smart, fast and reliable energy management is made possible by them. They help to control usage trends, prevent wastage and control on the usage of systems in one way or the other. Throughout my analysis, I came to the conclusion that any company that has a goal to minimize its energy consumption and operating costs should take these as factors to be considered.
With such features as real time data, automation, AI, and even the Internet of Things the future looks even more promising. In my opinion, it is not only reasonable but also a necessity to consider investing in PLCs based energy systems as something not only sensible to pursue but also a necessity for long term success.