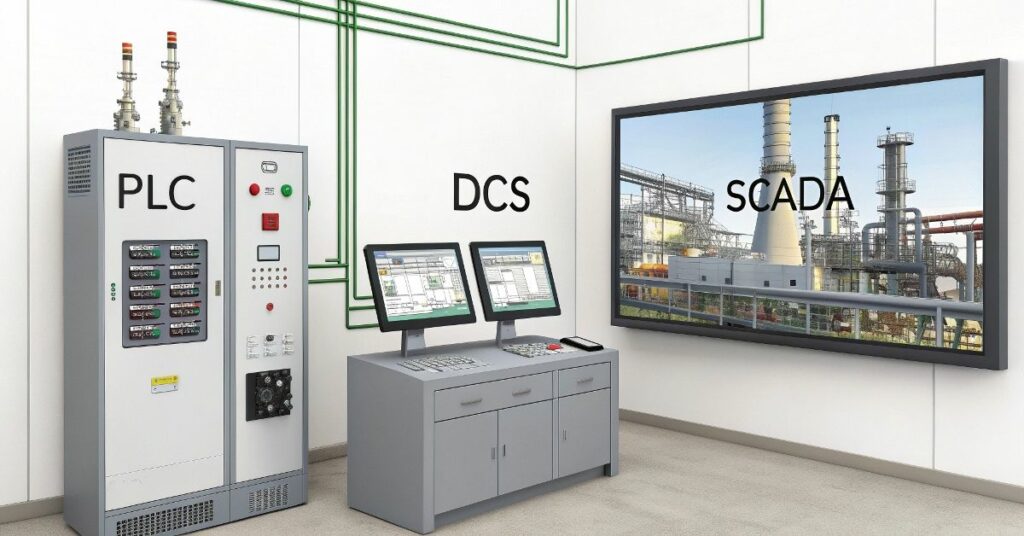
Three control systems which industries use are PLC and DCS and SCADA. The Programmable Logic Controller or PLC serves as a mechanism to control processes and machines. The Distributed Control System controls entire large complex systems. Remote monitoring and equipment control functions through continuous supervision of operations is achievable with SCADA (Supervisory Control and Data Acquisition).The implemented systems allow industrial work to function in safe and efficient ways.
The decision-making basis is determined by operational requirements yet every system has distinct advantages. Different automation systems have specific suitability for either small machines or industrial manufacturing facilities. Correct selection of the appropriate system offers reductions in costs and improved operational results.
PLCs are suitable for rapid execution of basic operations. The implementation of DCS suits operations that contain numerous control loops in large processing plants. The most suitable application of SCADA technology occurs during situations that require remote monitoring and control functionality. A detailed examination will help determine which system provides the best solution for your control system.
Introduction to Industrial Automation Systems
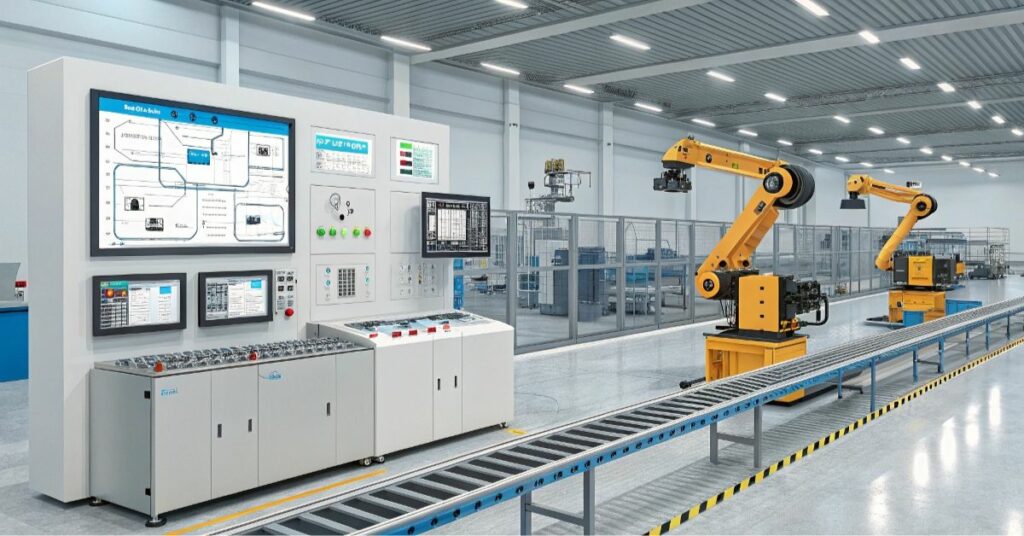
Operation of machines becomes more automatic through industrial automation systems which reduce human involvement. Controls are operated by computers combined with sensors that work through control devices. Industrial facilities use automation systems to create work that proceeds at higher speeds while maintaining safety standards besides achieving precise results. Through automation a company can generate greater output using minimal human resources.
The world adopts numerous automation systems for its operations. Some control simple machines, while others handle large, complex processes. Three commonly used automation systems consist of PLC and DCS in addition to SCADA. The industry becomes more efficient because each system performs a unique operational function.
What is a PLC and How Does It Work?
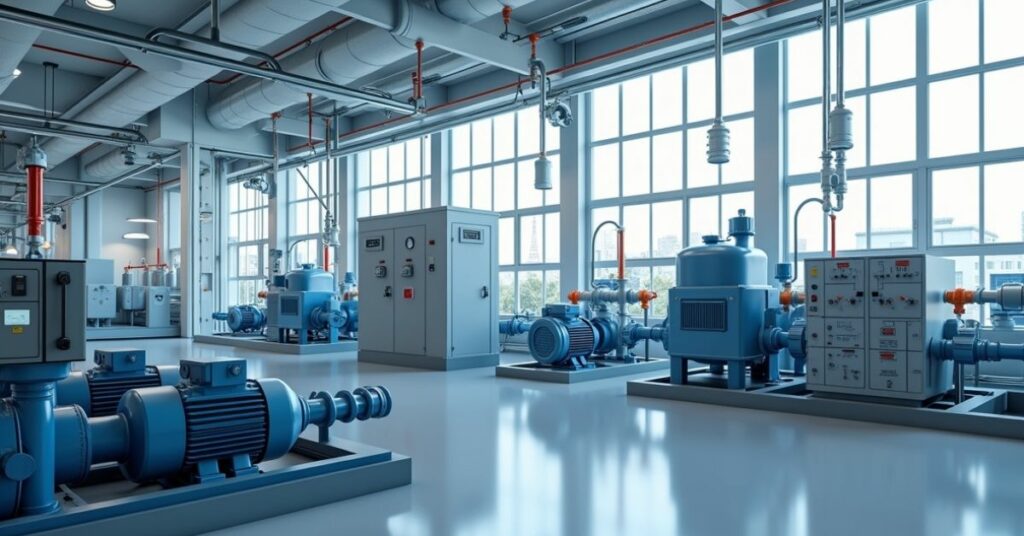
PLCs represent small computers which function as machine controllers. The device exists primarily for operations within industrial factories as well as other challenging environments. Similar to other computers the PLC obtains sensor data then analyzes it before forwarding results to motor or illumination controllers. Through their design PLCs enable automatic unattended operation of machinery.
Engineers prepare programs that PLCs execute to perform their operations. Through its program the PLC receives instructions regarding its operational functions under different circumstances. A sensor detecting a box on a conveyor belt enables the PLC to activate the motor which drives its movement. A step-by-step process at a high speed operates through an interface which allows for quick modification of its activity.
Understanding DCS: Features and Functions
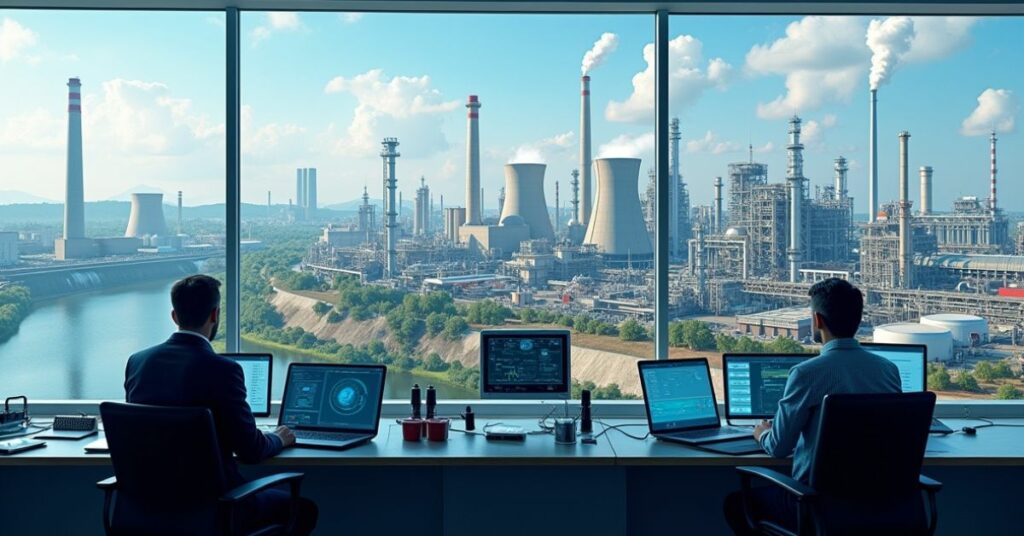
A DCS (Distributed Control System) serves as the control mechanism for big and complex industrial processes across multiple controllers. A DCS distributes its multiple controllers throughout the system network. Plants achieve control of different operational sections through interconnected controllers. Power plants along with chemical factories and oil refineries constitute the major applications of DCS systems.
Through DCS operators can ensure a steady process operation with safe control parameters. A system gathers data before verifying it and afterward performs intelligent decision-making activities. Users can monitor all process activities through screens that provide them with the ability to adjust settings when required. The DCS control system provides optimal performance to systems which require steady and enduring temporal management.
SCADA Explained: Role in Monitoring and Control
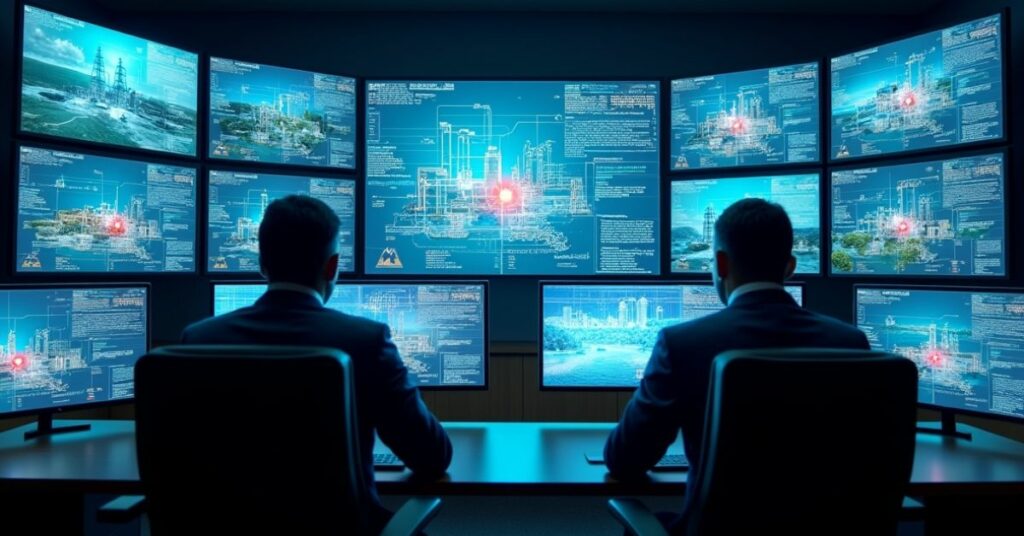
SCADA (Supervisory Control and Data Acquisition) the remote equipment control system provides capabilities to monitor equipment through distant operations. One of the key functions of SCADA involves gathering information from equipment which is transmitted to a main computer system. Through an operator screen both equipment data and machine controls are visible for operational purposes. Water plants and power grids together with transportation systems implement the use of SCADA systems for control purposes.
The monitoring system allows operators to identify and resolve issues swiftly through its functionality. The system saves information alongside its warning signals that instantly reflect current events. The system attains greater reliability and safety when implemented. The best application of SCADA technology occurs when it supports distributed operations spanning wide areas containing distant machines that require centralized monitoring.
Key Differences between PLC, DCS and SCADA
Work requirements establish which systems need selection. Fast operations together with small machines require a single PLC system. The DCS system demonstrates powerful capabilities when used in managing continuous operations that handle factories including chemical facilities and power generation facilities. Remote control operations extending across oil pipelines and water supply networks receive their optimal functionality through the SCADA technological system.
Here are some key differences:
- PLC controls machines directly and works very fast.
- DCS manages large systems with many control loops.
- SCADA helps monitor and control machines from far away.
- PLC and DCS are used more for control, while SCADA is mostly for monitoring.
- DCS is more centralized, while PLC is often used for single tasks.
- SCADA gives real-time data and alerts for quick action.
Choosing the Right System: Use Case Scenarios
The selection of proper technology requires an understanding of the required work activity. A PLC system functions optimally when managing quick operations for short machines. The continuous operation of big manufacturing plants benefits greatly from the use of DCS systems. SCADA functions ideally for remote monitoring and command applications such as water supply systems and oil pipelines.
Here is the table where you can see information about it:
System | Best For | Example Use |
PLC | Fast and simple machine control | Packaging machine, conveyor belt |
DCS | Large, continuous processes | Power plant, refinery |
SCADA | Remote monitoring and control | Water treatment, electric grid |
FAQ’s
What stands out as the essential difference which divides PLC and DCS from SCADA?
PLC controls machines, DCS manages big processes, and SCADA is used for remote monitoring and control.
Which system should I use for a small machine?
A PLC is the best choice for simple and fast control of small machines.
Does SCADA possess the capability to handle machine operations or limits its function to observation?
SCADA can monitor machines and send control commands from a distance.
Conclusion
Industrial automation depends on the operation of PLC and DCS in addition to SCADA. Every one performs unique functions according to its purpose. PLC delivers quick performance on quick small operations. DCS provides the optimal solution when dealing with big and continuous operations. SCADA permits the supervision and management of industrial processes remotely. The knowledge of how each system performs enables you to select better solutions.
The system choice must align with the requirements you need to address. The foundation of your decision depends on process dimensions alongside control requirements and machine location. You will achieve faster work with better reliability by selecting suitable systems that match their designated functions.