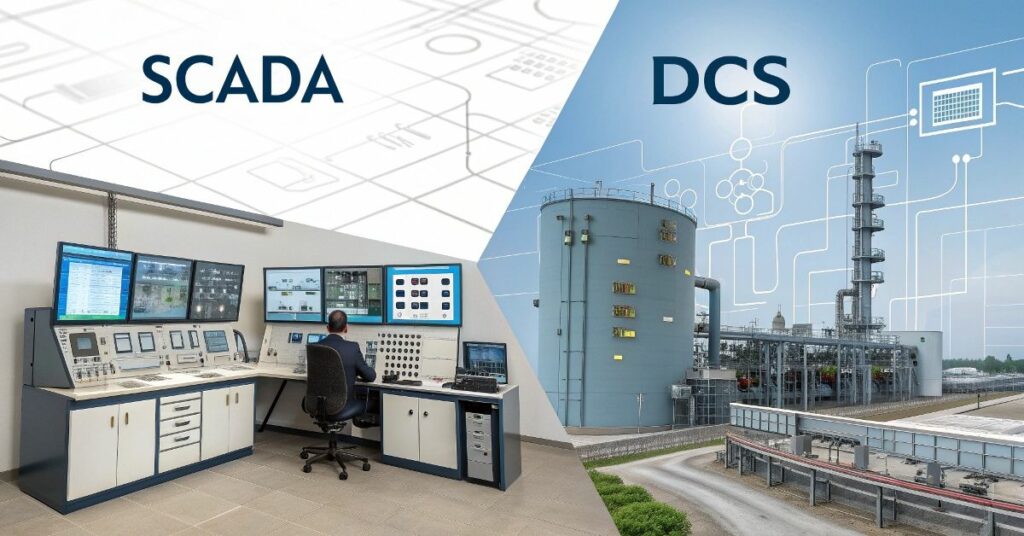
The acronym SCADA represents Supervisory Control and Data Acquisition systems. A central operator uses this technology to supervise and manage equipment and process operations. DCS means Distributed Control System. The system operates in real time for managing complex large industrial facilities. The systems serve different purposes in industrial automation although they operate differently from one another.
The selection between implementing SCADA or DCS systems creates a difficult decision for organizations. The selection depends on the specific requirements you have for a system. SCADA offers users flexibility as their main reason to select this system. Multiple organizations select DCS since continuous control functions best within the system. Both systems come with different characteristics and specifications so we will explore them to determine the best fit for your requirements.
The wide application areas of SCADA include power grid control and water treatment systems. DCS provides better performance in chemical and oil plant systems. The primary emphasis of SCADA systems stems from data gathering functions whereas DCS systems excel at managing process operations directly.
Understanding SCADA and DCS Systems
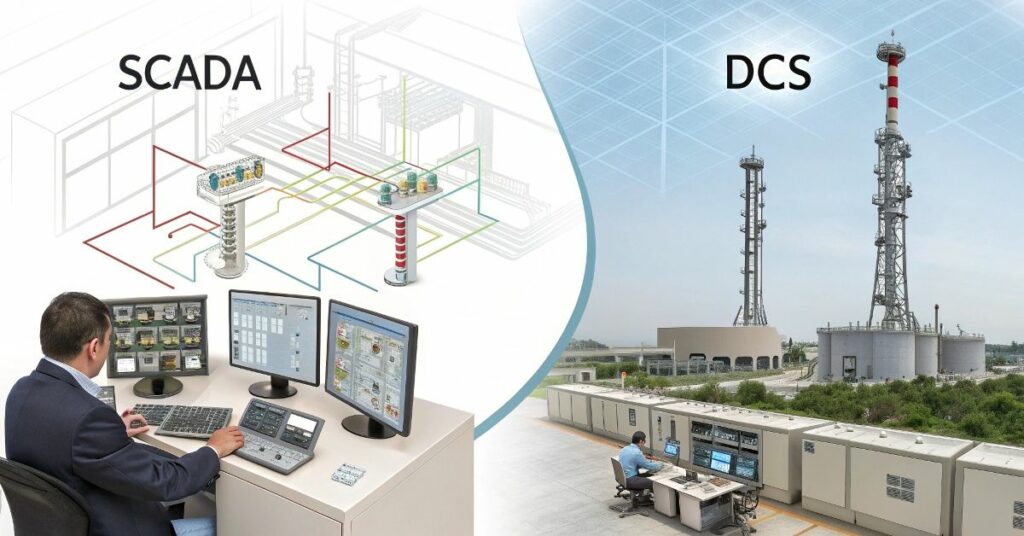
The industrial system control and monitoring functions can be performed by both SCADA or DCS systems. SCADA enables operators to monitor machines through a central control station. The system gathers information which it displays through screens. The process receives direct control from DCS systems which work optimally when located in a single spot. The system provides commands to machines while also maintaining system stability.
The implementation of SCADA occurs in power plants together with water systems and remote locations. DCS operates frequently in oil refineries as well as chemical plants and factories. Safety improvements and time benefits and human error reduction are features common to both systems. Understanding their operational principles enables users to select the best system solution for their requirements.
Key Components and Architecture Differences
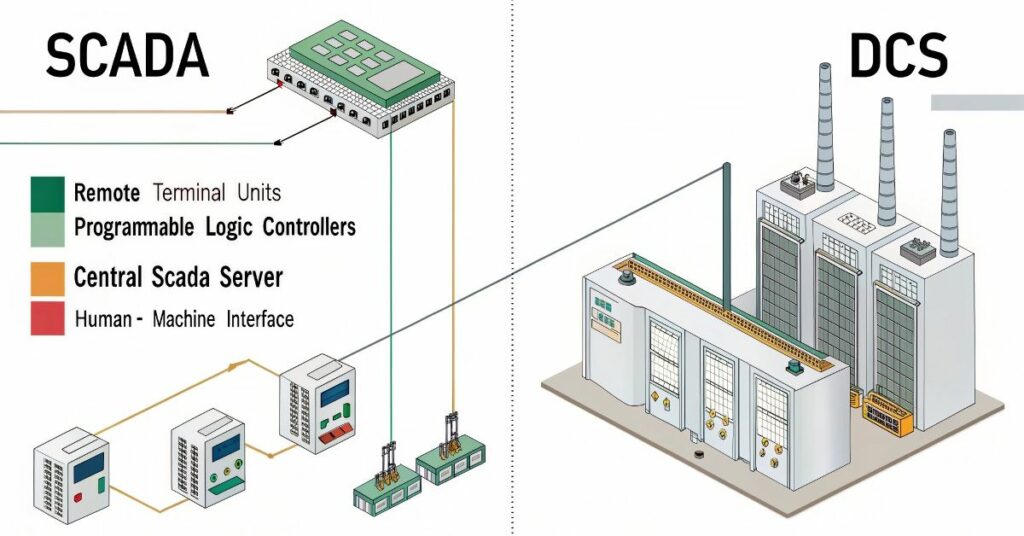
A SCADA system includes sensors together with remote terminal units (RTUs) and one central computer. The remote terminal units function to gather data which it then transmits to the control center. Operators manage the system by using software that provides both visibility and control features from a distant location. The distribution control system SCADA operates effectively across extensive territory systems.
DCS systems consist of controllers together with sensors and a control server. The controllers serve as proximity devices to the machines. The control systems execute their task assignments rapidly and directly. DCS functions as a centralized system from a single point while providing easy control functions. The system provides optimal performance for continuous processes with multiple interrelated operations.
Operational Scope and Application Areas
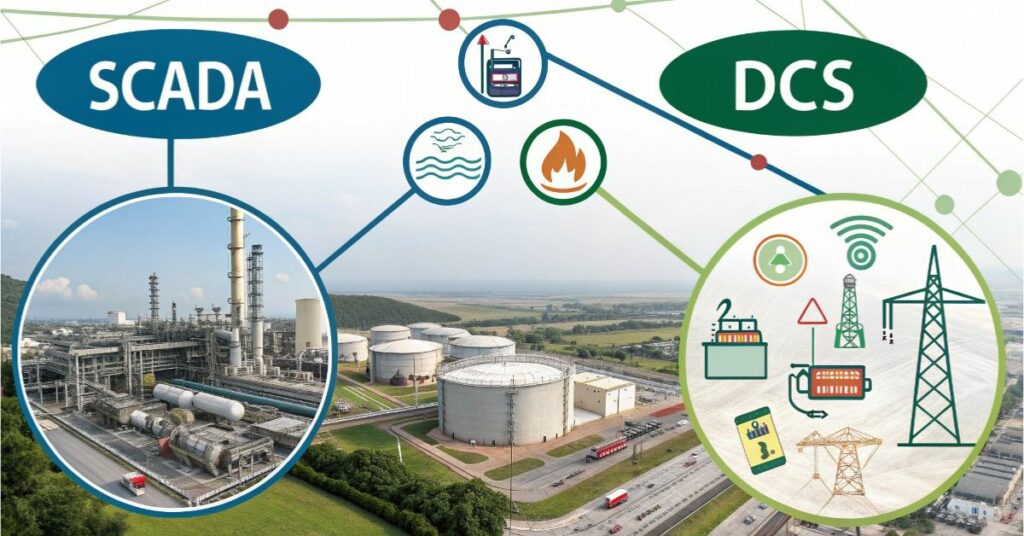
The most efficient operation of SCADA systems occurs within extensive geographical areas. Operation centers use SCADA to supervise and regulate equipment from unified locations. This system provides excellent capabilities for data collection along with alert notification. The operator can benefit from SCADA to monitor activities throughout various locations.
Common uses of SCADA:
- Water treatment plants
- Electric power grids
- Oil and gas pipelines
- Traffic control systems
Stable and speedy control operations work best with DCS systems. The DCS system delivers outstanding results when controlling complicated continuous processes that demand rapid and precise control actions. The implementation of DCS occurs when operators require complete process control.
Common uses of DCS:
- Chemical plants
- Oil refineries
- Food and beverage factories
- Pharmaceutical production
Performance and Response Capabilities
The SCADA system functions as a surveillance tool which distributes data to operating personnel. The system delivers live data yet might react slower than necessary during certain situations. The system functions effectively whenever instant responses cannot be guaranteed. The resolution of system issues in SCADA systems requires human intervention for their resolution.
The control provided by DCS grants quick responses in addition to enhanced operational authority. The system operates without routine delays when facing changes within its systems. Smart controllers located near the process enable its operation. Steady tasks and complex applications benefit from this system design because it ensures higher reliability
Scalability and Flexibility in Integration
The adaptability of SCADA allows for quick and simple scaling of its operations. SCADA systems provide scalability for either big or small installations which allows expansion and addition of new components whenever needed. The system allows effortless addition of new devices and sensors. SCADA systems excel at linking various types of equipment in a network.
The DCS system performs best for maintaining continuous operations of particular steady procedures. The capacity of SCADA for integration exceeds that of other systems. DCS provides strong system control for complex technology networks with many components. DCS serves processes requiring specialized control that does not require substantial expansion capabilities.
Cost, Maintenance and Complexity
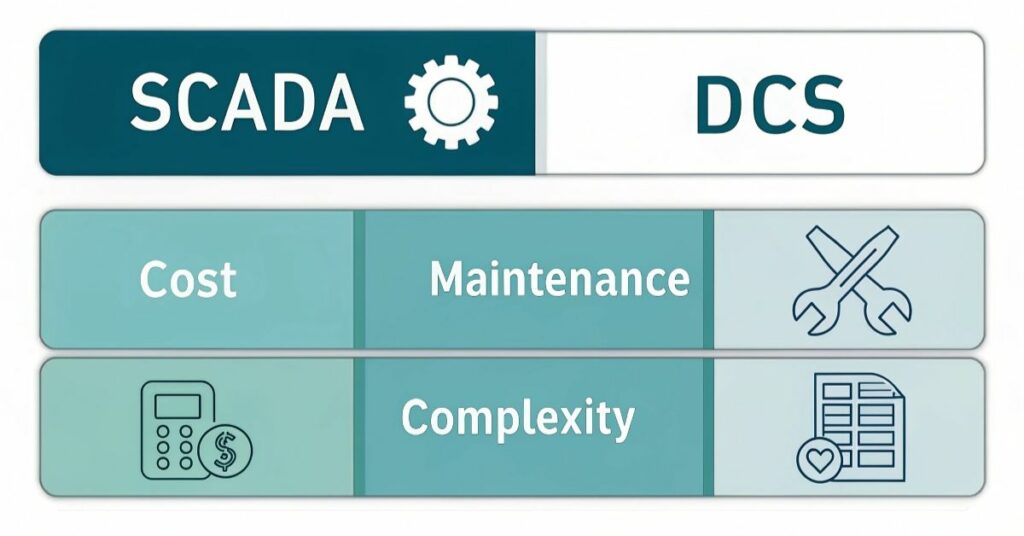
Initial implementation of SCADA systems costs less money. These systems possess simple design and perform basic maintenance operations efficiently. The adaptability of SCADA allows it to suit various operational requirements. The sustained expenses are likely to rise as the quantity of networked devices and areas expands.
The installation costs for DCS systems exceed those of other systems. Special equipment along with control systems represent necessary requirements for their operation. The cost of system maintenance becomes more challenging and upgrades tend to be expensive. DCS delivers dependable and fast operation solutions for controlling extensive and complicated systems.
Factor | SCADA | DCS |
Cost | Lower setup cost | Higher setup cost |
Maintenance | Easier and less expensive | More complex and costly |
Complexity | Less complex and more flexible | More complex but highly reliable |
Which One Fits Your Industry Best?
Firms operating wide distribution systems benefit most from using SCADA as their monitoring solution. The system delivers successful results for water treatment installations and power grid systems and oil pipeline operations. SCADA provides superior data tracking capabilities for locations that are distant from each other. The system provides versatility which enables it to manage different equipment and systems.
A continuous production environment requires DCS systems as the better operational solution. The system offers optimal solutions to chemical plants alongside oil refineries and factories that require real-time smooth control systems. Reliable and quick process adjustments require a DCS system because it delivers superior control and stability.
FAQ’s
What distinguishes DCS from SCADA as control systems?
The purpose of SCADA involves remote process monitoring across broad areas while DCS operates to directly control single-location processes.
What stands as the most suitable technology for implementing remote monitoring systems?
SCADA is better for remote monitoring since it can cover large distances and connect multiple sites.
Which system should be used for elaborate procedures?
The control system of DCS provides better performance for managing complicated continuous operations that need swift and accurate control.
Conclusion
The selected control system for your operations depends on your specific needs between SCADA or DCS. SCADA serves as a reliable system for tracking extensive networks across broad areas and data acquisition. The basic manufacturing industries find successful and cost-effective operations through the use of SCADA. The most beneficial use of DCS emerges when industries require precise process control and immediate system responses in chemical plants and refineries.
Your business requirements will guide you toward choosing either SCADA or DCS as your control system. Wide-area systems require SCADA control systems because they excel at monitoring whereas DCS works best in managing localized complex operations. Your system selection process needs understanding of these systems to fulfill operational requirements.