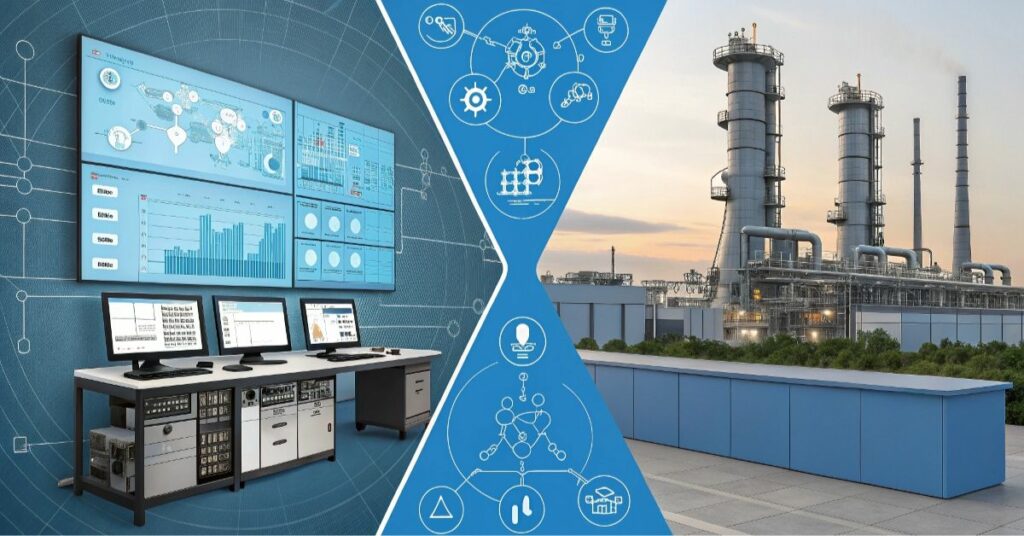
The operational activities of industries depend on control systems including SCADA and DCS implementations. SCADA stands for Supervisory Control and Data Acquisition. DCS means Distributed Controls System. Industrial processes are monitored by two collaborative systems although each system performs its own unique task.
Various industrial operators fail to distinguish between the control systems. Both systems do comparable work although they execute controls through distinct mechanisms in separate operational settings. Understanding their distinction enables you to adopt the correct system according to your requirements. This article will explain the distinctive features of these systems.
The wide-area water supply systems and power distributions operate under systems. The functional area for DCS is limited to manufacturing facilities and industrial plants. Data collection serves as the main function of SCADA yet DCS prioritizes process control capabilities.
What Is SCADA?
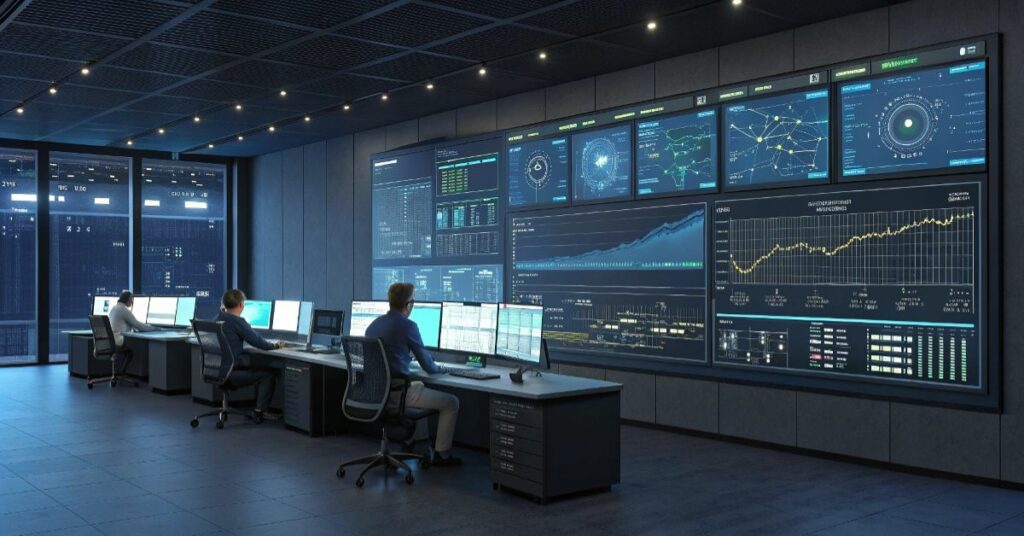
SCADA stands for Supervisory Control and Data Acquisition. The system enables remote monitoring together with control functionality for machines or equipment which operate from a central location. The system receives live data which originates from diverse operational areas of the process. Operators view process information through screens enabled by systems. When issues occur, provide warning notifications which direct personnel to solve the problems efficiently.
This serves as the monitoring system for industries including water treatment as well as electricity generation and oil gas operations. This system enables business operations to become more efficient and safer. The remote distance control of the SCADA system enables on-site operators to be reduced to minimum levels. The combination of these advantages leads to decreased costs and time requirements as well as better performance from humans.
What Is DCS?
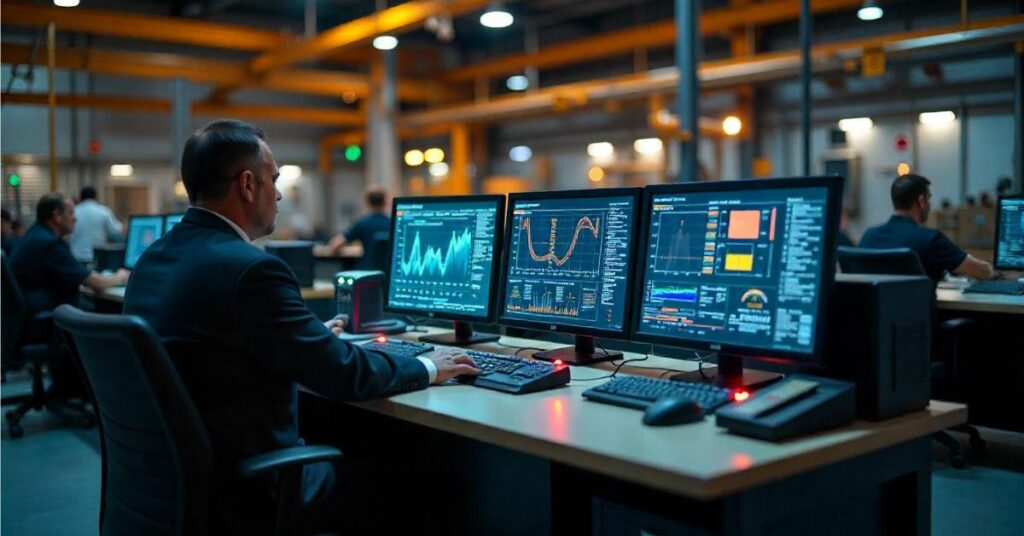
DCS functions as a control mechanism specifically designed to regulate operations existing inside one bounded area whether it be a factory or power plant. The production area contains numerous controllers that operate near the machinery components. Multiple controllers function as a united system by overseeing different process elements within the system.
The Distributed Control System offers effective control for sophisticated as well as continuous process operations. The system provides real-time control capabilities to its operators. Such control systems enable operators to perform changes and maintain stability while avoiding system shutdowns. The combination of DCS systems provides improved operational excellence along with enhanced safety features to chemical plants and refinery operations.
Core Functions of SCADA vs. DCS
The systems managed through SCADA and DCS have operating and monitoring features with different approaches to execution. Due to its extensive coverage capabilities it provides better system surveillance across wide regions. Systems located in a single space require better control performance from DCS implementations. Every system carries particular essential operational functions.
SCADA main functions:
- Collects real-time data
- Sends alerts during problems
- Controls equipment from a distance
- Stores data for reports
DCS main functions:
- Controls processes continuously
- Adjusts systems in real time
- Manages complex operations
- Keeps the system stable and safe
Architecture Differences between SCADA and DCS
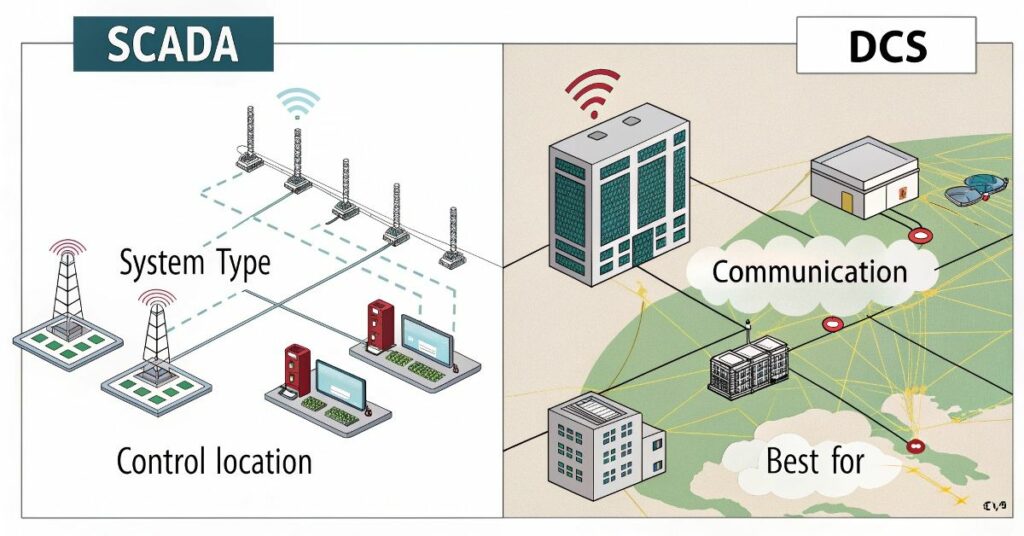
Many remote sites communicate through a centralized system configuration in SCADA. Long-distance communication links serve as the method for data collection in this system. The controllers at DCS operate near the production equipment because of its localized organizational structure. Local devices in this system connect through rapid and reliable connections inside the same operational boundary.
Differences:
Feature | SCADA | DCS |
System Type | Centralized with remote sites | Distributed and local |
Communication | Long-distance (radio, internet) | Fast local networks |
Control Location | Central control room | Controllers near equipment |
Best For | Wide-area systems | One-site complex processes |
Where SCADA and DCS Are Typically Used?
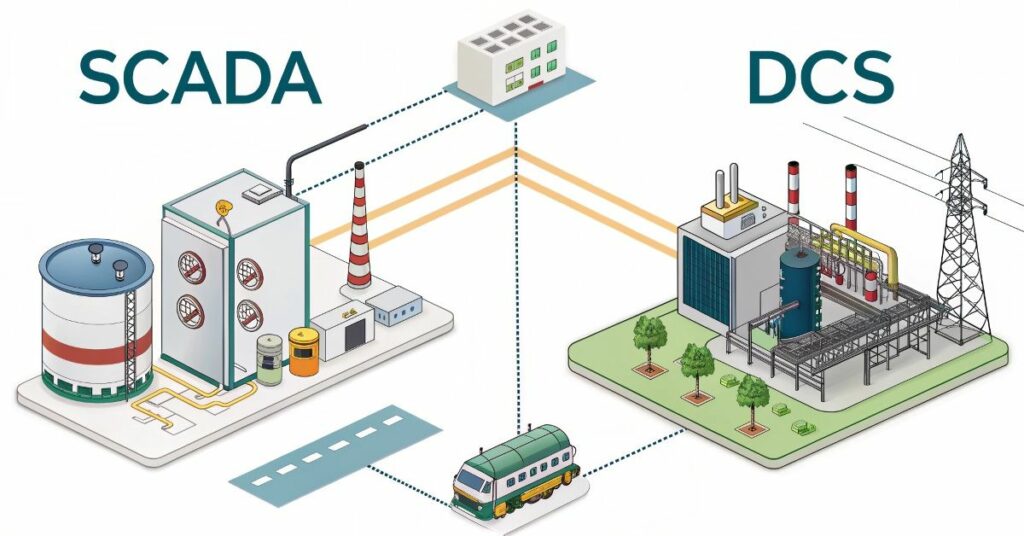
The application of SCADA systems lies mainly within extensive coverage systems. The monitoring systems control water supply networks while managing power grids and operational conduits of oil pipelines in addition to managing traffic systems. The distributed control system enables remote monitoring and control thus providing an optimal solution for wide-ranging outdoor and geographically separated systems.
The Distributed Control System (DCS) remains focused on a single installation base such as factory or plant environments. The system finds application within chemical plants together with oil refineries, power stations and food production facilities.
Can SCADA Replace DCS (or Vice Versa)?
The two systems have separate functions thus non-one can take over the role of the other. The wide area monitoring and system control properties of SCADA systems make them superior to other options. A single operating venue shows better results when using DCS control systems.
The two systems possess the ability to integrate their operations in particular scenarios. The results would probably not be optimal when using only one system rather than the other. The system choice depends upon the work nature and involved space scale together with control requirements.
Final Verdict: Is SCADA the Same as DCS?
These control systems differ even though they provide monitoring and control functions for their respective infrastructure. These systems follow distinct operations methods for various application sites. Wide-area control belongs to SCADA systems whereas DCS systems perform local detailed control operations.
The individual strengths among these systems exist independently. Through remote access SCADA provides excellent data collection functionality. The control capabilities of DCS systems surpass those of technology because of their ability to conduct real-time control of complex industrial processes. Learning about these systems’ unique features enables users to make proper selection decisions that suit the work requirements.
FAQ’s
Is it possible to combine the capabilities of SCADA with DCS systems?
Yes, some industries use both to get the benefits of wide-area monitoring and detailed control in one system.
The question arises about which system offers better capabilities between SCADA and DCS?
It depends on the job. The choice depends on the system requirements because SCADA serves remote operations while DCS manages complex locally based processes.
Do the operational functions of SCADA systems and DCS appear comparable?
The two systems share identical organizational objectives although they implement operations through distinct methods. The main function of SCADA systems involves monitoring whereas DCS systems handle process control activities.
Conclusion
The industrial environment relies on both SCADA and DCS systems. These systems enable user supervision for maintaining safe process operation and steady system functions. Different tasks and environmental conditions require dedicated systems though they have similar appearances.
Your industrial demands determine whether you should choose SCADA or DCS. A wide-area system stands as the most suitable solution. The appropriate control technology for managing multi-component systems in one geographic area is DCS. These two distinct systems allow you to select effective operational solutions.