HVAC failures often start with sensor malfunctions. Sensors send important data to the Building Management System (BMS). When they fail or give wrong readings, the whole system can act up. This results in difficulties with temperature control and unnecessary use of energy which influence your comfort and finances.
Another common problem is equipment overloads. When parts like compressors or fans work too hard, they wear out quickly. If the system is overloaded, it can break down suddenly and cost a lot to fix. The BMS helps spot these issues early to avoid bigger damage.
Many HVAC problems are caused by poor airflow. If airflow is not proper, the system works harder and becomes less efficient. Issues including these can be caused by dust, dirty air filters or vents that are closed off. If you detect airflow issues fast, both your air quality and the system’s performance are protected.
Table of Contents
ToggleUnderstanding Building Management Systems (BMS) and HVAC
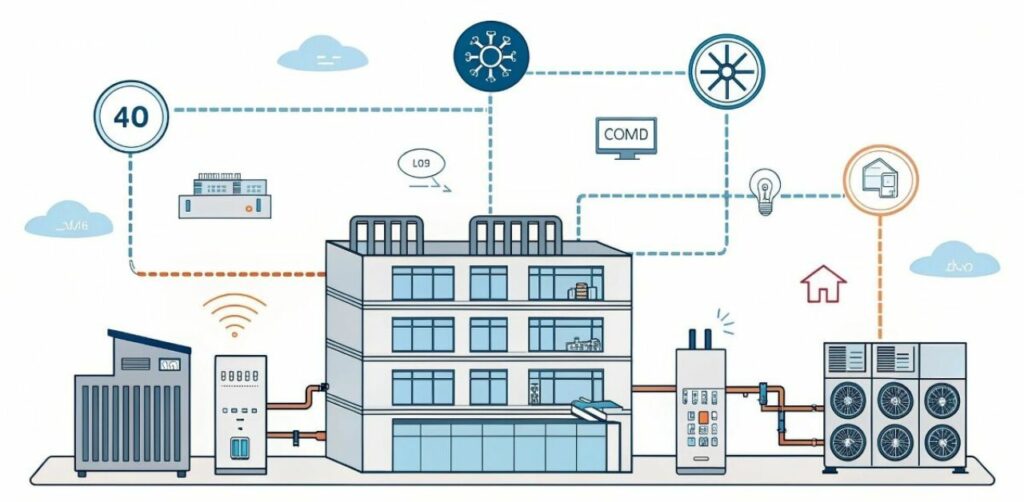
HVAC equipment is continuously monitored by a Building Management System (BMS). It records temperature, pressure and equipment condition to maintain smooth operations. With this, the BMS helps ensure the home is comfortable and energy is not wasted. Monitoring the system, it catches any early signs of any problems.
Early detection through the BMS is key to avoiding costly repairs and long downtime. When problems pop up, the system alerts technicians right away. This quick response means issues can be fixed fast. Therefore, the buildings are kept comfortable and the HVAC systems function well for a long time without unexpected failures.
Why Sensor Malfunctions Are Critical to Catch Early?
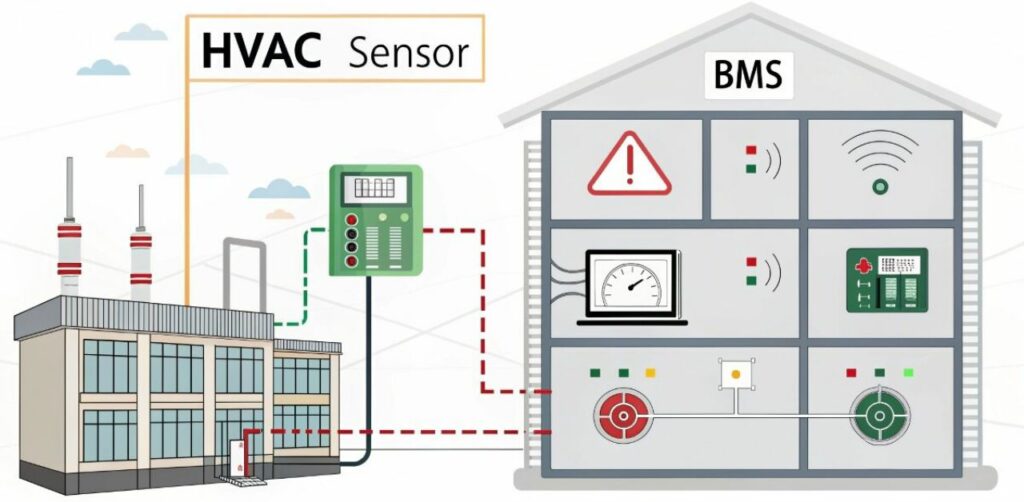
Faulty sensors send wrong information to the HVAC system. This causes the system to work inefficiently. For example, the system may heat or cool too much, wasting energy. Eventually, this can cause costs to go up and make the area less comfortable. For this reason, you should pay attention to sensor problems as soon as you see them.
Quick alerts from the BMS allow for fast repair of sensors. A sensor that malfunctions can be quickly recalibrated or replaced by technicians. The system runs well and uses less energy because of this. Doing something early on stops problems from growing bigger.
- Faulty sensors cause wrong temperature readings
- Inefficient HVAC operation wastes energy
- Early detection leads to fast repairs
- Saves money on energy and maintenance
- Helps maintain building comfort and air quality
Identifying Equipment Overloads and Their Impact
Overloads put extra pressure on motors and compressors. When they run beyond their limits, parts wear out faster. Because of this stress, the system could overheat, shut down or even fail completely. It is often expensive and takes a lot of time to address these problems.
The BMS helps prevent this by tracking energy use in real time. It spots unusual spikes in power that signal overloads. With quick alerts, maintenance teams can step in before serious damage happens. This keeps equipment safe and running longer.
How Airflow Issues Affect HVAC Efficiency?
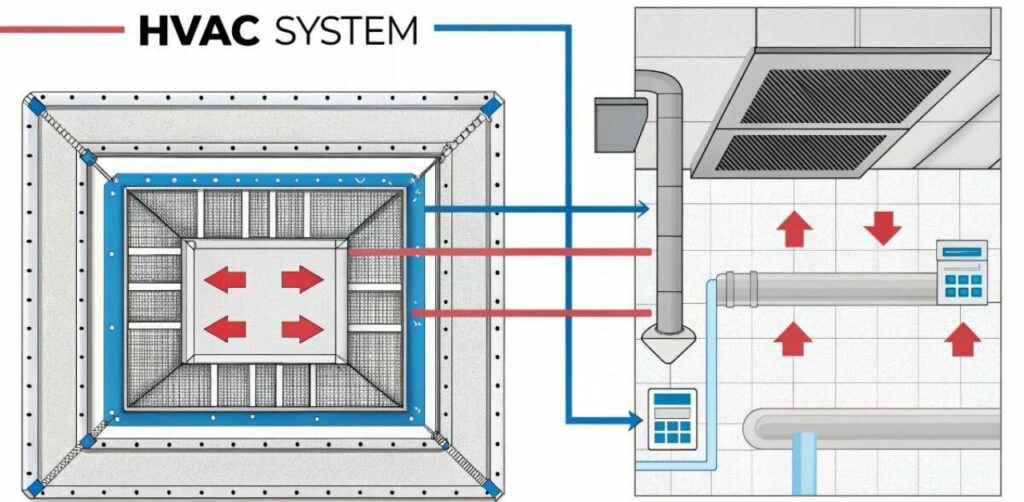
Blocked or leaking ducts make it hard for air to move through the system. This lowers heating and cooling performance. Some rooms may feel too hot, while others stay cold. If airflow is poor, the system has to put in extra effort and use more energy which lowers comfort.
Finding airflow problems early helps keep temperatures steady and air clean. The BMS tracks pressure levels and fan speeds to spot trouble fast. With quick action, technicians can fix leaks, clean filters, or adjust dampers.
Airflow Issue | Impact on HVAC | Solution |
Blocked ducts | Uneven room temperatures | Clean or remove obstructions |
Leaking ducts | Energy loss, poor airflow | Seal or replace damaged areas |
Dirty filters | Reduced airflow, strain on fans | Replace filters regularly |
Closed or stuck vents | Weak air circulation | Inspect and open vents |
Benefits of Proactive HVAC Failure Detection via BMS
Finding problems early makes it less likely for equipment to break down suddenly. It makes expensive emergency fixes less necessary. If problems are found early, it stops motors, fans and compressors from decaying. It makes the HVAC system last longer and saves you money in the future.
It works to maintain the same temperature inside which makes it comfortable. The BMS makes changes to settings according to what is happening in real time. There will be no cold or hot areas, less complaining and improved indoor air quality. Both people and the system are comfortable and everything works better each day.
Best Practices to Optimize BMS for HVAC Monitoring
Keep sensor calibrations and system software up to date. This ensures accurate readings and smooth performance. Old data or outdated software can cause delays or false alerts. Regular checks help the BMS stay reliable and efficient.
Also, make sure staff know how to act when alerts come in. Quick responses prevent small issues from turning into big problems. Train teams to read data correctly and take fast action. This keeps the system running well and avoids unnecessary downtime.
FAQ’s
What are the most common HVAC failures detected by BMS?
Sensor problems, equipment working too hard and trouble with the flow of air are the three main HVAC issues detected by BMS.
How does a BMS help prevent HVAC system breakdowns?
BMS monitors HVAC performance constantly and alerts users to any early signs of problems, cutting down the chance of unexpected breakdowns.
Why is detecting sensor malfunctions important for HVAC systems?
Sensors provide critical data, and catching malfunctions early keeps the HVAC running efficiently and saves energy.
Conclusion
Spotting HVAC issues early helps systems work smoothly for a longer period. Problems such as sensor errors, overloads and issues with airflow are detected with the help of a BMS. Fast repairs can cut costs, use less energy and stop major problems from happening.
A properly maintained BMS looks after both temperature and efficiency. By staying proactive and training staff, buildings stay cooler in summer, warmer in winter, and more cost-effective all year round.